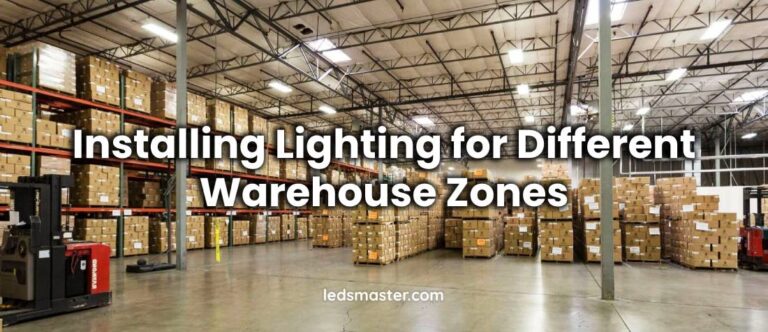
Imagine a warehouse where optimal lighting enhances safety and productivity. Effective installation transforms the space into a vibrant and efficient workspace, making it beneficial to master the process, whether retrofitting or designing anew.
Get your complimentary lighting design today
Effective lighting not only enhances visibility but also contributes to overall operational efficiency. Well-lit warehouses facilitate smoother workflows, minimize accidents, and promote a positive atmosphere for employees. To achieve optimal results, understanding the various stages of lighting installation is imperative.
Table of Contents
ToggleBefore embarking on the installation process, a thorough assessment of the warehouse layout is necessary. Understanding the dimensions and design of the space allows for effective planning of the lighting system. Each warehouse is unique, with specific areas dedicated to different functions, such as storage, picking, and packing. Evaluating these areas helps determine the specific lighting requirements based on the nature of activities taking place.
Taking detailed measurements of the warehouse will assist in calculating the necessary light distribution. Identifying high-traffic zones, including loading docks and assembly areas, ensures that these locations receive adequate illumination. Moreover, accounting for obstacles like shelving units and equipment is crucial to avoid shadowing and dark spots.
Establishing the lighting needs of a warehouse involves evaluating the specific tasks performed within the space. Different activities require varying levels of illumination, which can be quantified in lux. For instance, areas designated for detailed work, such as packing stations, typically require higher lux levels compared to general storage areas.
In addition to lux levels, it is essential to consider the color temperature of the lighting. Cooler temperatures can enhance visibility and alertness, while warmer temperatures create a more relaxed environment. This assessment helps create a tailored lighting plan that addresses the functional needs of the warehouse.
Establishing a budget is a fundamental aspect of the planning process. Understanding the costs associated with lighting fixtures, installation, and ongoing maintenance is vital for making informed decisions. Analyzing various lighting options and their associated costs ensures that financial resources are allocated effectively.
Investing in energy-efficient lighting solutions can lead to long-term savings on electricity bills, offsetting initial installation costs. Evaluating potential incentives or rebates for using energy-efficient technologies can further enhance the budget. Careful consideration of both upfront and operational costs helps in selecting the most suitable lighting system for the warehouse.
Preparing for installation involves gathering the necessary tools and equipment. Common tools required for lighting installation include ladders, wiring tools, and safety gear. Ensuring that all equipment is in good working condition contributes to a smoother installation process.
Checking the availability of electrical supplies, such as wiring and connectors, is equally important. Having all materials on hand prevents delays and interruptions during installation, allowing for a more efficient workflow.
Adhering to safety protocols during the installation process safeguards both the workers and the facility. Proper safety gear, including gloves, helmets, and eye protection, should be worn to minimize the risk of accidents.
Additionally, implementing lockout/tagout procedures when working with electrical systems prevents unintended energization of circuits. Proper training on safety practices ensures that all personnel involved in the installation are aware of potential hazards and how to mitigate them.
In many cases, collaborating with qualified electricians or lighting specialists enhances the quality of the installation. Professionals bring expertise in electrical systems and installation techniques, ensuring compliance with local codes and regulations.
Engaging experts also allows for a more thorough evaluation of the warehouse’s lighting needs. They can offer insights into the latest technologies and trends in warehouse lighting, ensuring that the selected solution is both effective and future-proof.
Determining the placement of lighting fixtures is a critical aspect of the installation process. Proper positioning ensures optimal coverage and minimizes shadowing. Fixtures should be installed strategically in relation to the activities taking place in each area of the warehouse.
In high-traffic areas, such as loading docks and pick zones, increased illumination is necessary to enhance safety and visibility. Conversely, storage areas may require less intense lighting. Conducting a detailed light level calculation for each section of the warehouse facilitates informed decision-making regarding fixture placement.
Once the fixtures are positioned, the next step involves wiring and electrical setup. Connecting fixtures to power sources requires careful attention to detail. Ensuring proper grounding and secure connections is vital for safe operation.
Before proceeding with wiring, it is crucial to turn off the electrical supply to avoid accidents. Following the manufacturer’s wiring guidelines ensures compatibility and functionality. Additionally, using appropriately rated wiring for the fixtures being installed enhances safety and performance.
Mounting fixtures is a crucial step in the installation process. Depending on the type of fixture, mounting methods may vary. For ceiling-mounted fixtures, following the manufacturer’s instructions for secure installation is vital.
Using the right hardware for mounting ensures stability and reduces the risk of fixtures falling. Proper alignment and leveling of fixtures contribute to even light distribution throughout the warehouse. Conducting a final check of all mounted fixtures ensures that they are securely in place before proceeding.
After the installation is complete, testing the lighting system is essential to confirm functionality. Turning on the lights allows for immediate verification of the setup. Any flickering or malfunctioning fixtures should be addressed promptly to avoid disruptions in warehouse operations.
Conducting adjustments to the fixtures may also be necessary to achieve the desired illumination levels. Fine-tuning the angle or height of fixtures can enhance light distribution and minimize shadows. Observing the lighting in action during peak operational hours provides insights into any further adjustments that may be required.
Once the installation is complete and the lighting system is operational, conducting final inspections ensures that all components function as intended. Checking for compliance with safety standards and regulations is vital for maintaining a safe working environment.
Reviewing the lighting layout against the initial plans allows for verification of fixture placement and overall effectiveness. Any discrepancies should be addressed promptly to optimize the lighting system’s performance.
Educating staff on operating and maintaining the lighting system enhances overall efficiency. Training sessions should cover topics such as fixture operation, emergency protocols, and basic troubleshooting.
Ensuring that employees are familiar with the lighting system fosters a sense of responsibility for its upkeep. Providing guidance on reporting issues, such as flickering lights or burned-out fixtures, promotes proactive maintenance.
Keeping detailed records of the installation process is advantageous for future reference. Documentation should include information such as fixture specifications, wiring diagrams, and maintenance schedules.
Having comprehensive records available facilitates troubleshooting and maintenance in the future. This information can also aid in evaluating the performance of the lighting system and planning for potential upgrades.
Establishing a regular maintenance schedule ensures that the lighting system continues to operate at peak performance. Routine inspections should be conducted to check for any signs of wear or malfunction.
Cleaning fixtures and lenses regularly helps maintain optimal light output. Dust and debris can accumulate over time, diminishing the effectiveness of the lighting system. A consistent maintenance routine prolongs the lifespan of the fixtures and enhances overall illumination.
Identifying and resolving common lighting issues contributes to uninterrupted warehouse operations. Flickering lights, for instance, may indicate loose connections or faulty fixtures. Addressing these issues promptly helps maintain a safe working environment.
If a fixture burns out, replacing it with a compatible unit ensures continued functionality. Regularly checking and replacing any burnt-out bulbs minimizes disruptions and maintains consistent lighting levels throughout the warehouse.
As technology advances, considering upgrades to the lighting system may become necessary. Newer lighting solutions often provide enhanced energy efficiency and improved performance. Evaluating the existing system against available options ensures that the warehouse remains competitive and cost-effective.
When planning an upgrade, assessing the return on investment is crucial. Energy-efficient fixtures may have a higher upfront cost, but the long-term savings in energy bills can offset this initial expense. Engaging professionals for upgrades ensures that the new system is installed correctly and operates optimally.
Proper installation of warehouse lighting not only improves visibility but also enhances safety and operational efficiency. From the initial assessment of the warehouse layout to the final inspections after installation, each step plays a vital role in achieving optimal results. By focusing on careful planning, appropriate fixture selection, and thorough installation procedures, a well-lit warehouse can significantly impact productivity and employee satisfaction. Regular maintenance and attention to potential issues will ensure that the lighting system continues to perform effectively over time, contributing to the overall success of warehouse operations.